Key Takeaways:
- Reliability engineers play an essential role in ensuring equipment reliability and preventing downtime in various industries.
- They possess a combination of technical and analytical skills and a deep understanding of reliability analysis principles.
- Reliability engineers identify and mitigate risks, optimize the life cycle of equipment, and improve the reliability and performance of assets.
Risk Management and Mitigation
As a reliability engineer, one of my key responsibilities is to identify potential risks associated with equipment failure and develop strategies to mitigate those risks. This involves conducting risk assessments and implementing reliability improvement initiatives that reduce the likelihood of failure and minimize the impact of any failures that do occur. In order to manage risks effectively, it is important to have a thorough understanding of the equipment and its failure modes. This requires collaboration with subject matter experts and data analysis to identify patterns and trends. Once potential risks have been identified, I work to develop preventive maintenance strategies that address those risks and minimize downtime. Reliability engineering plays a critical role in risk management by ensuring that equipment is designed, operated, and maintained to meet performance requirements and avoid catastrophic failure. By utilizing reliability improvement strategies, we can improve equipment reliability and minimize the impact of any failures that do occur. Some of the techniques I use for risk management and mitigation include:- Failure mode and effects analysis (FMEA)
- Reliability-centered maintenance (RCM)
- Statistical process control (SPC)
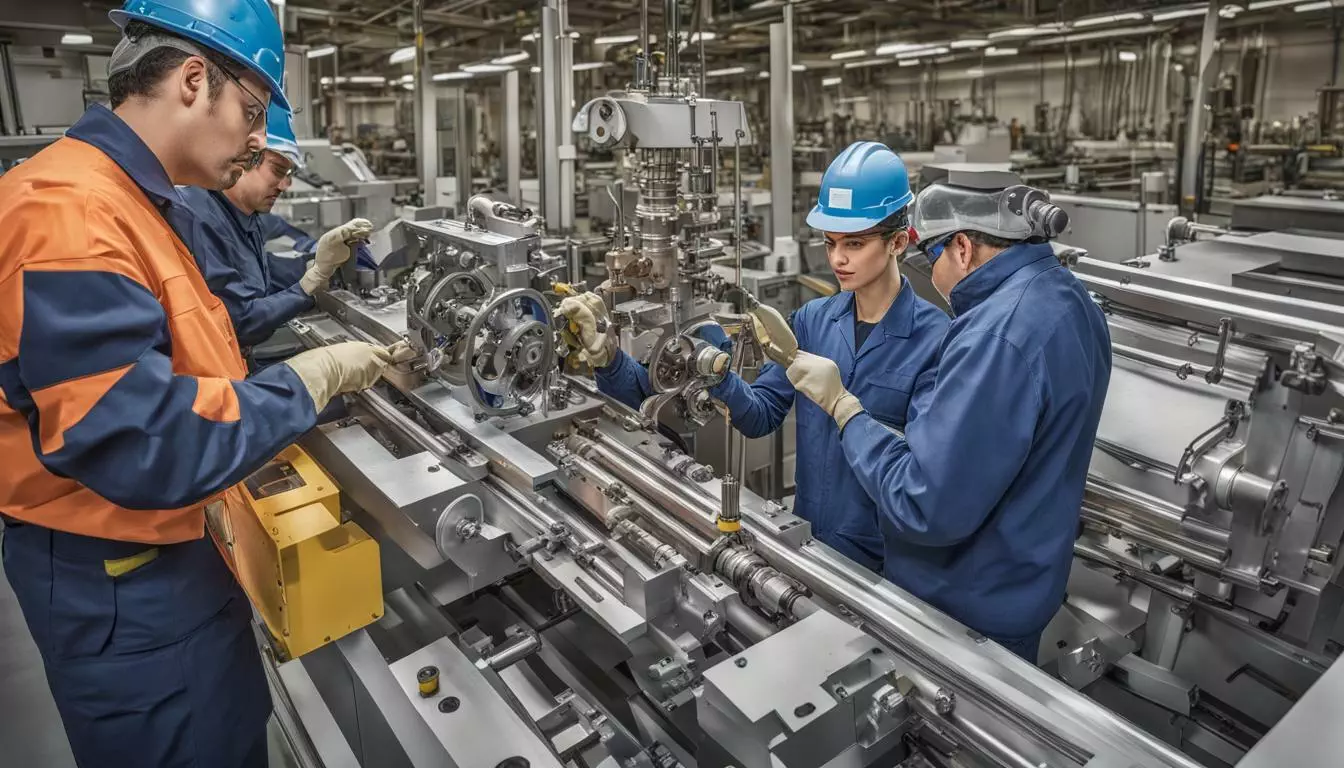
“Effective risk management and mitigation is essential for ensuring the reliability and availability of critical equipment.”
Life Cycle Optimization
As a reliability engineer, one of my primary responsibilities is to optimize the life cycle of equipment. This involves developing maintenance strategies that minimize downtime, extend the useful life of assets, and maximize return on investment. By implementing effective maintenance optimization programs, companies can reduce costs, increase productivity, and improve equipment reliability. To achieve life cycle optimization, reliability engineers must first understand the criticality of the equipment they are responsible for. This involves devising strategies to assess equipment performance, including monitoring and analyzing critical data points. Using this information, we can determine how often maintenance is required, when equipment needs to be replaced, and what type of maintenance activities are most effective. Maintenance optimization is not a one-time event; it requires continuous analysis and improvement. Reliability engineers use advanced analytics and modeling techniques to predict and prevent equipment failures. This includes using reliability-centered maintenance (RCM) to identify the most critical components and develop maintenance tasks that can be performed on an as-needed basis. By prioritizing maintenance activities, companies can reduce unnecessary maintenance costs while ensuring the availability and reliability of critical assets. Reliability engineers also use predictive maintenance technologies, such as vibration analysis and thermography, to identify potential equipment failures before they occur. By detecting early warning signs of equipment degradation, we can initiate proactive maintenance activities to prevent equipment failures and extend the useful life of assets. This approach is more cost-effective than reactive maintenance, which can result in costly downtime and repairs. Overall, life cycle optimization is an essential function of reliability engineering. By developing effective maintenance optimization programs and leveraging advanced analytics and modeling techniques, reliability engineers can ensure the availability and reliability of critical assets while minimizing costs and maximizing return on investment.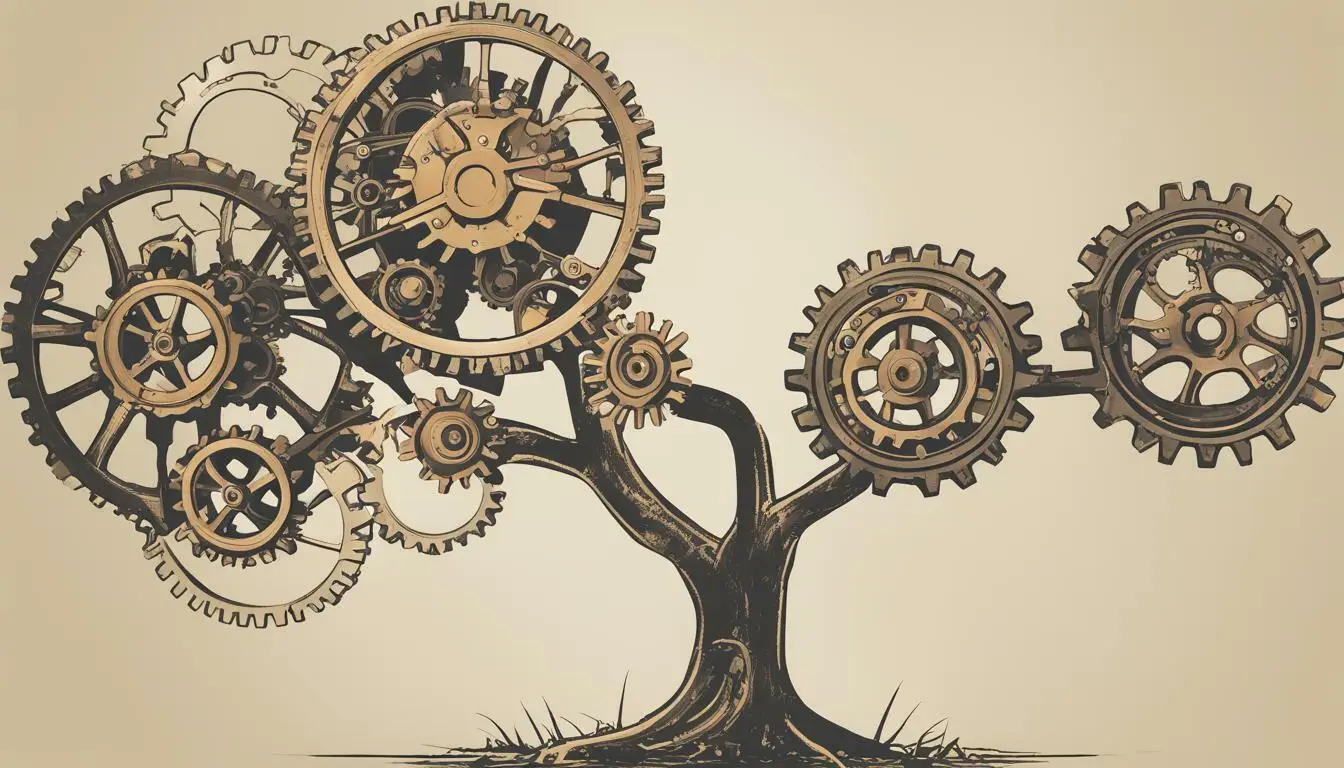
Failure Analysis and Root Cause Identification
As a reliability engineer, one of my primary responsibilities is to conduct thorough failure analysis to determine the root cause of equipment failures. This involves collecting and analyzing data on the equipment’s performance, maintenance history, and operating conditions. By identifying the underlying causes of the failure, we can develop effective strategies to prevent future occurrences. This includes implementing corrective actions and developing preventive maintenance plans. Reliability analysis also plays a crucial role in failure analysis. By analyzing reliability data, we can identify patterns and trends that reveal potential failure modes and enable us to develop targeted strategies. One common technique used in failure analysis is the “5 Whys” methodology. This method involves asking a series of “why” questions to drill down to the root cause of the failure. For example, if a machine fails, we would ask why it failed. If the answer is because of a bearing failure, we would then ask why the bearing failed. This process continues until we have identified the root cause. Overall, failure analysis and root cause identification are critical components of reliability engineering. By identifying and addressing the root causes of failures, we can improve equipment reliability, minimize downtime, and increase the overall efficiency of our operations.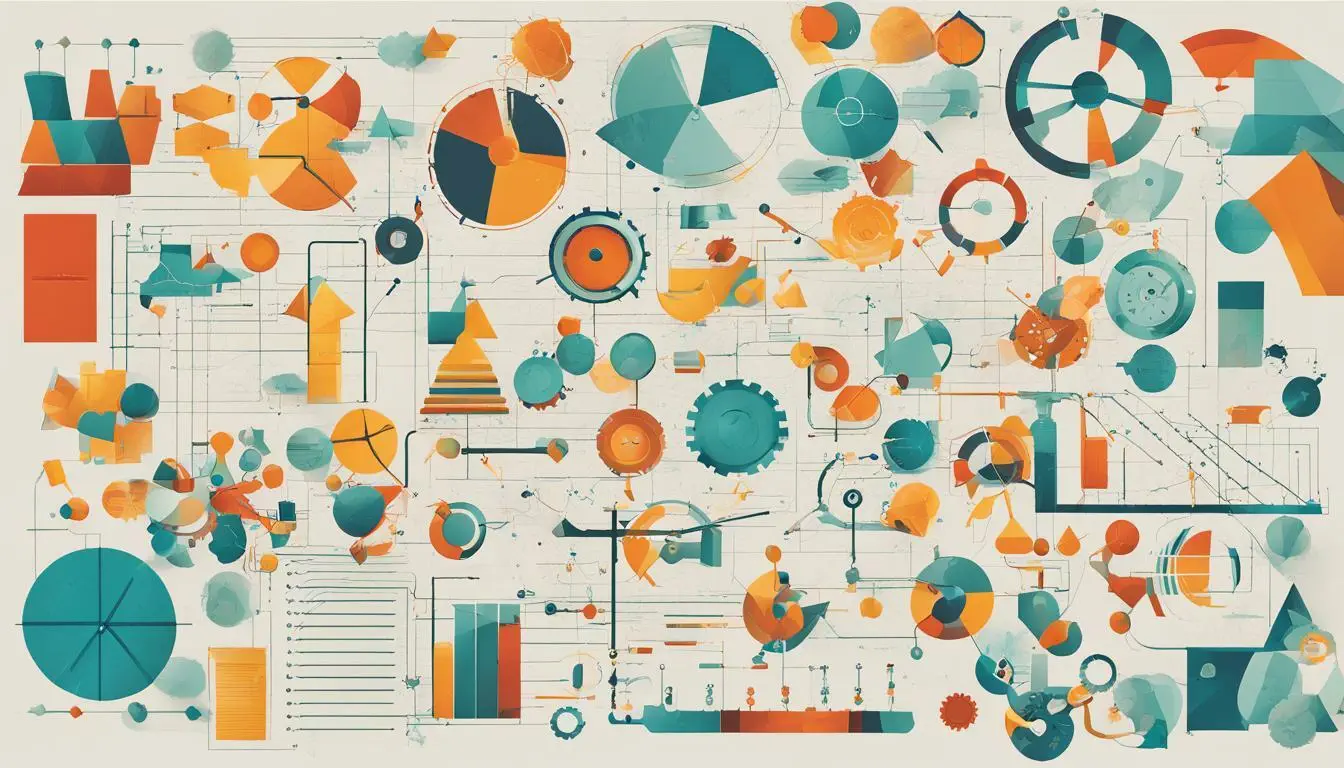
Reliability Testing and Performance Evaluation
One of the key responsibilities of a reliability engineer is to design and conduct reliability tests to evaluate the performance of equipment. Reliability testing is crucial to assess the reliability of assets throughout their life cycle and identify any potential issues that may lead to failure. The type of reliability testing conducted may vary depending on the industry and specific equipment being tested. Some common types of reliability testing include:- Environmental testing
- Functional testing
- Stress testing
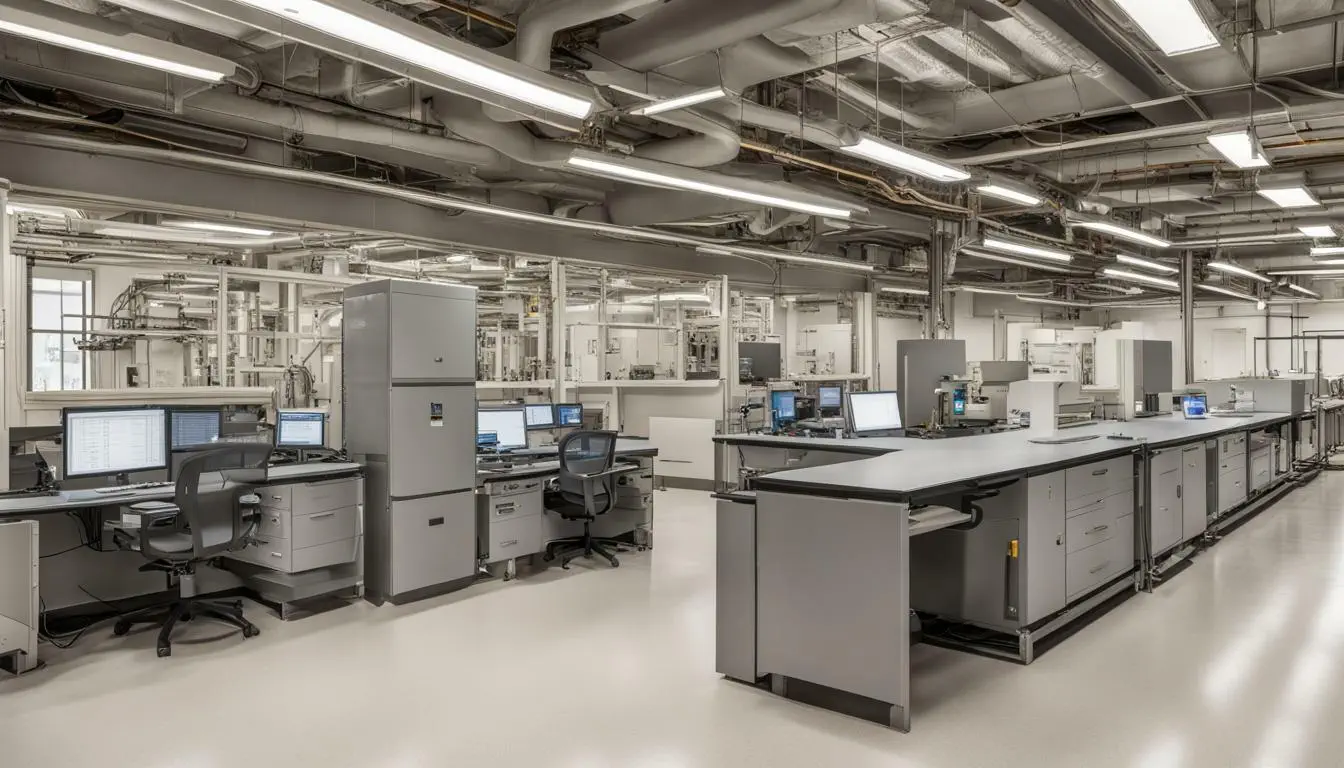
What Are the Similarities and Differences Between AWS Developer and Reliability Engineer Roles?
The roles and responsibilities of AWS developers and reliability engineers intersect at some points, but there are significant differences between the two. Both positions require the use of AWS technology, but their primary focus varies. Essentially, an AWS developer’s main responsibility is to conceptualize and implement software solutions using AWS services. On the other hand, a reliability engineer’s principal task is to ensure the stability, reliability, and superior performance of the system.
Asset Management and Optimization
As a reliability engineer, asset management and optimization are crucial to maximizing the performance and reliability of equipment. Effective asset management involves creating comprehensive asset management plans that outline strategies for maintenance, repair, and replacement. Reliability modeling techniques are used to predict equipment failure and develop maintenance strategies that minimize downtime and extend the life of assets. Reliability engineers utilize a variety of tools to optimize asset performance, such as the Reliability Centered Maintenance (RCM) methodology. This approach uses a systematic process to identify potential failure modes and select the most appropriate maintenance strategy to mitigate the risk of failure. Another important aspect of asset management is the use of Condition Based Maintenance (CBM) techniques. These techniques involve monitoring equipment performance in real-time, using various sensors and data analysis tools. By tracking the performance of critical assets, reliability engineers can detect equipment issues early on and implement maintenance strategies to prevent downtime.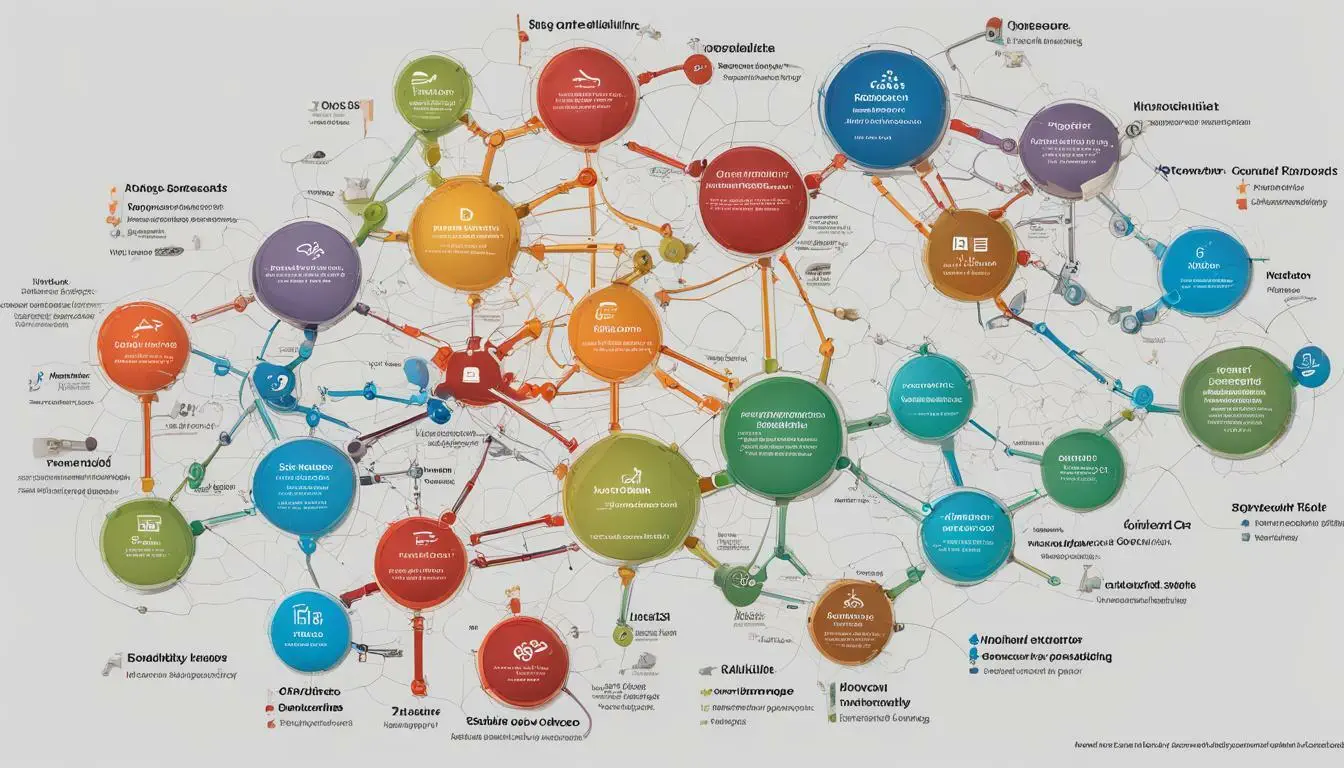